Case Study:
Sustainable Recycled PET Content
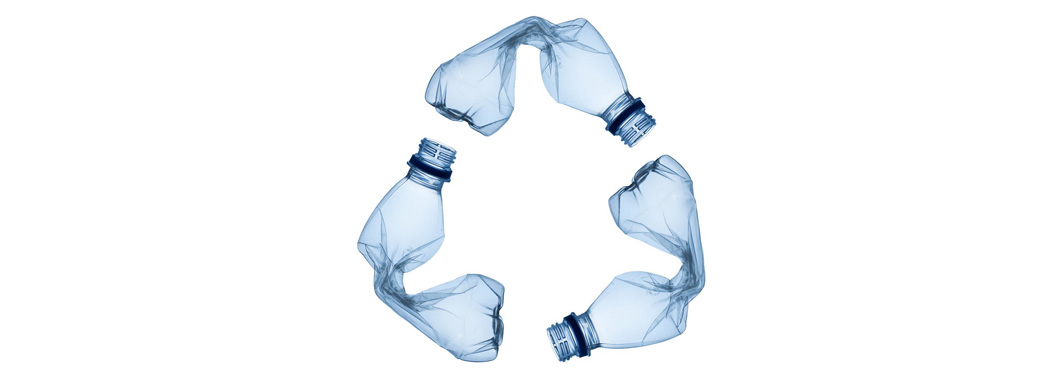
Recycled content in plastic containers is common today. Like most developments, getting there required overcoming a number of technical challenges.
One of my contributions was to determine the effect of repeated processing passes for the recycled material. We were worried that it was not just a matter of getting the material to work in the first pass. If we were to be successful, the bottles had to be recyclable over and over again. We invented a multi-pass protocol to show how the quality of the material degraded over multiple passes at high concentrations. A mountain of work went into this, but in practice we learned the main degradation step is the first one – all of the subsequent passes incrementally add to color degradation, but none so dramatic as the first. Today we know that if we can make an acceptable bottle that passes at 50% or higher recycle content, it will be acceptable to use in future cycles of the same resin. We also had to establish quality standards for the recycled material. Accepting truck-loads of washed bottle flake was too high of a risk without some quality standards in place. We had to establish how much moisture we could tolerate, how much residual adhesive could be in the material, what a proper color and IV standard should be, as well as making sure the supplier maintained their equipment and process. All of these procedures were floating in the industry, but we had to organize them and get the supply chain to agree to use them. It was not easy telling some of the people that had scrap selling in the DNA to raise the quality bar. Decontamination and FDA protocols followed the first launch of PET into rigid packaging. Initially the market was tested by the liquid soap brands, but eventually we knew we had to put recycled content into food grade applications. Further, PTI had an idea to use small particle size to enhance the decontamination process mandated by the FDA protocol. Truth be told, I would drink any product out of a good clean washed PET flake from the suppliers we use today. But, the FDA is not satisfied with that standard. We have to prove that our process can take out any nasty chemical that some consumer might store in a bottle before returning it for recycling, and we have to assume that 100% of the consumers might do the same thing. Decontamination is a temperature dependent permeation problem. We were smart enough to get the scientists that could predict the outcome to drive the conditions we used to build our process. It really was a terrific success and one of the first simulation success stories I was lucky enough to work on.